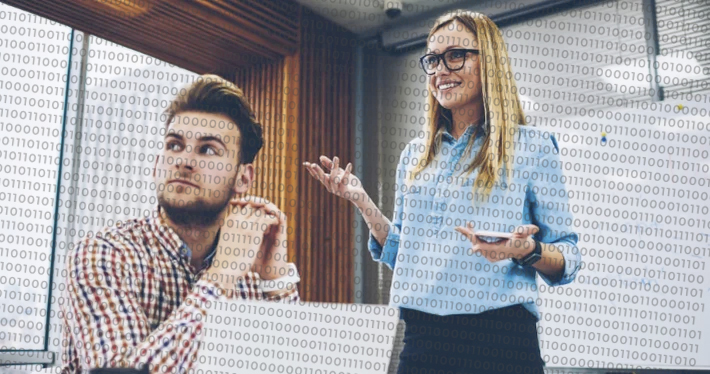
Digitalization of Quality and HSE: The preliminary steps
1) Evaluate the current situation of your information system
First of all, it is about make an assessment of the current situation. What solutions exist within your organization? Which ones are most commonly used? Do you have an ERP (Enterprise Resource Planning), HRIS (Human Resource Information Software) software?
In this assessment, it is essential to understand what the key data is for your business and how to retrieve it. The chosen digitization solution will replace your existing tools and facilitate feedback on the ground. However, some data will have to be extracted from other software. So before you start, I recommend that you check the interface possibilities. with your existing software. A key point to avoid unnecessary data recopying in your digitization project.
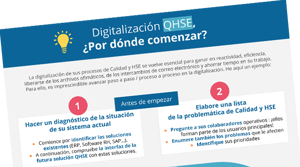
2) Establish a list of Quality and HSE issues
Then, it is about establish a list of your Quality and SHE issues, as well as an order of priority. What are the main difficulties in my daily work? What are the priority projects for this year? Take the time to think about all of these questions.
The role of a digital tool is above all to facilitate your daily work.
It is also essential ask your collaborators about their own problems in the field. You will be one of the main users of the solution. However, Remember that the Quality and HSE field is everyone's business and that each employee has a potential interest in accessing the solution. If tablets/smartphones facilitate the entry of information in the field, the tool must be as intuitive as possible. so as not to waste time on training in the use of the software. In fact, the most difficult part will perhaps be accompanying the change and the adoption of the solution by the most reluctant.
You have taken it upon yourself to establish an evaluation of your system and to take into consideration your problems as well as those of your collaborators.
But now the question is: where to start?
Here is an example of a possible digitalization scenario for Quality and HSE.
1) The GED (Electronic Document Management)
For your Quality system to be as efficient as possible, a Structured GED It is a "must have".
There is nothing worse than realizing in the middle of an audit that a field procedure version is out of date!
Thanks to digital technology, Follow the life cycle of your documents directly in the tool. You have a complete history of the modifications made. Once the GED is digitized, It is time to associate all types of documents (procedure/record/instruction) with the different applications of the tool.
2) The global action plan
The action plan is the core of your Quality and HSE system. It allows you to regularly follow up on the actions to be taken and in turn continuously improve your system. Digitize your plan of action means offering better data exchange within your organization. Each employee follows the actions assigned to them. They are mainly alerted when one of them expires.
Once the action plan has been digitized, Actions resulting from your future audits/visits (or follow-up of your non-conformities/deviations) are automatically uploaded into the global action plan without having to re-enter each action.
3) Management of security audits/visits
Paper is a problem when it comes to perform audits or visits. In fact, it is synonymous with many transcriptions (and therefore the risk of losing information!). Equipped with a tablet and/or smartphone, You can use your digitalized forms directly in the field, even without an Internet connection ("offline" mode). You have the possibility to consult your procedures already loaded in the tool (through prior integration of the GED).
Once the audit is completed, The PDF report is automatically generated and sent to your employees by email. In your overall action plan you will find the various actions resulting from the audit/visit in question.
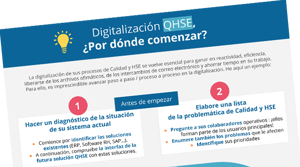
4) Monitoring of non-conformities/deviations
Apart from carrying out audits/visits, as Quality and HSE personnel, it is sometimes difficult to keep everything under control. Sometimes we miss events taking place on the ground. A very simple example: failure of one of the production lines, non-conformity/deviation sheets are not available on the shop floor. Employees do not transcribe the information on paper. The line restarts without the Quality and HSE department being informed of the failure.
A digitalized form would have allowed field workers to enter information directly into the tablet in real time. without having to print new non-conformity sheets or call the Quality and HSE department. You will be notified by email of any line failure that occurs in the field and of any corrective measures that have been implemented by the workshop manager.
Digitize on the fly or all in one go?
As mentioned above, some processes need to be digitalized as a matter of priority. And today, the best way to achieve this digital transition is to go step by step. For example, start by digitizing the GED and the action plan, then the audits. The formulas proposed by the editors of Quality and HSE are adapted to your request and your work.
Furthermore, the more your structure grows, the greater the need for digitalization: The solution must adapt to these new demands. Digitalization will make it easier to manage your system, especially in multi-site contexts.
You now have all the cards in hand to carry out your digitalisation project. Make sure you define your priorities and don't hesitate to go gradually so as not to risk getting lost in the process.
Fuente: https://www.blog-qhse.com/es/la-digitalizaci%C3%B3n-de-calidad-salud-seguridad-y-medio-ambiente-qhse-c%C3%B3mo-hacerla